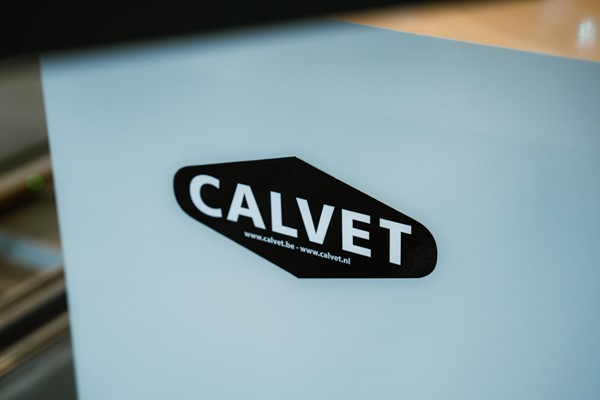
custom-made machine
Calvet (BE)
Cross-pollination. That's what happens when two creative machine builders join forces. To inject more automation into the production of aluminium windows and doors, Calvet wanted to develop its own series machine. CNC Solutions helped develop and implement the concept.
Unique in the industry
‘We mainly supply machines to produce windows and doors. We are now building a machine that can combine different operations and actions such as assembly, gluing, pressing, checking,’ explains business manager Stefan Nees. ‘It will be unique in our industry. Today, to assemble a window, a corner press is used. A process that still involves a lot of manual steps. We are going to bring all these steps - assembling, gluing, pressing, checking, cleaning - together at one central workstation that requires only one operator. A concept that will not only boost efficiency, but also the quality of finishing.’
Innovative ideas
For Nees, the input from the team at CNC Solutions was crucial. ‘We were stuck in our own concept. Their clear technical view put a different spin on it. Through their innovative ideas combined with our experience in how an angle press should work, we succeeded in our set-up,’ says Nees. Flexibility was at the top of the list of features for the machine. It had to be able to work with different types of profiles, formats, press positions and gluing techniques. Two six-axis robots therefore form the heart of the installation. The robots adjust their position according to the format, ranging from 300 to 4500 mm. They can also automatically change gripper according to the step in the production process.
Knowledge and technology
‘What is unique is the specially developed gripper to press the corners. That's really where Calvet's knowledge is in it,’ explains Lander Debruyne of CNC Solutions. But that also involved smart technology, from Beckhoff Automation. ‘Thanks to the new electric cylinders AA3000, we managed to put ‘feel’ into the machine. The operator prepares the frame on one of the carts. A sensor feeding the actuator measures whether all the pieces fit together properly before clamping and pressing. Feel free to compare it to an egg: gripping without breaking. Partly because of that built-in intuition, the bar for quality is so much higher.’
Simple and intuitive
A striking feature of the machine is the large screen next to it. ‘On it, the operator can follow everything. For us, Industrie 4.0 means making complex technology as simple and intuitive as possible. The operator scans the barcode and is shown the steps he needs to complete. He has just two buttons with which to navigate to the next or previous step. It couldn't be simpler.’ The intention is now to test the machine extensively in practice. ‘That experience will help us arrive at a truly standard machine. That there is a market for it, we are convinced. Wherever labour costs are high, automation is the answer,’ concludes Nees.
"Dankzij de vernieuwende ideeën van CNC Solutions in combinatie met onze ervaring, zijn we geslaagd in ons opzet"- Stefan Nees, Calvet